One stop hydraulic hardware product service provider Rotary Joint HYDRAULIC HOSE HOSE FITTING
WHAT ARE THE COMMON CAUSES OF HYDRAULIC HOSE FAILURE?
HYDRAULIC HOSE
8 min read
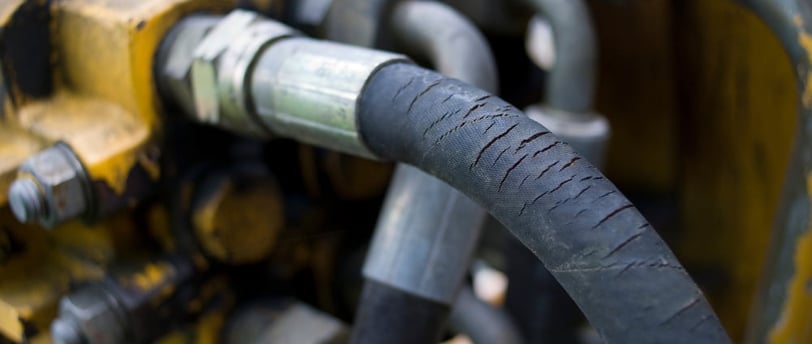
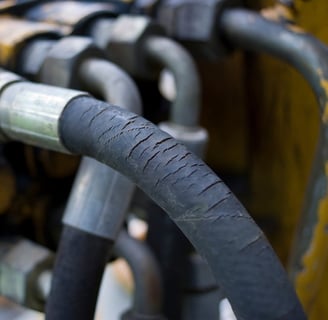
Whether it is today's common concrete transporter or the road roller excavator used in the construction of roads, or even the hydraulic system of the loader oil drill machine in the heavy industry can not be separated from the rubber hydraulic hose. In the process of use, similar faults such as seepage, cracking, cracking, loosening are also common; I have made a summary analysis of this. The hydraulic hose has multiple layers of steel wire braided or wound, each layer will fail and lead to the progress of the entire project. Here’s a detailed look at the factors you mentioned and how to mitigate hydraulic hose:
1. Aging and Wear
Causes:
- UV Light: Exposure to ultraviolet light can cause the hydraulic hose material to degrade and become brittle.
- Heat: High temperatures can accelerate the aging process, leading to softening, hardening, or cracking of the hydraulic hose.
- Ozone: Ozone exposure can cause the hydraulic hose to crack, particularly in areas of high stress.
Signs of hydraulic hose Aging:
- Cracks: Visible cracks on the outer surface of the hydraulic hose.
- Blisters: Bubbles or blisters that indicate internal damage.
- Hardening or Softening: Changes in the texture of the hydraulic hose material.
Mitigation:
- Regular Inspections: Conduct visual inspections regularly to identify signs of hydraulic hose aging.
- Protective Measures: Use protective sleeves or covers to shield hydraulic hoses from UV light and heat.
- Replacement: Replace hydraulic hoses that show signs of significant wear or aging.
2. Improper Installation
Causes:
- Incorrect Routing: Poor routing can lead to hydraulic hose kinks, twists, or excessive bending.
- Excessive Bending: Bending the hydraulic hose beyond its minimum bend radius can restrict fluid flow and cause premature wear or rupture.
- Inadequate Support: Lack of proper support or clamping can cause excessive movement and wear.
Signs of Improper Installation:
- Kinks and Twists: Visible kinks or twists in the hydraulic hose.
- Restriction: Reduced fluid flow or increased pressure drop.
- Damage: Signs of wear or damage due to rubbing or chafing.
Mitigation:
- Proper Routing: Ensure hydraulic hoses are routed to avoid kinks and twists, respecting the minimum bend radius.
- Support and Clamping: Use appropriate supports and clamps to secure hydraulic hoses and prevent excessive movement.
- Training: Ensure that installation personnel are trained in proper hydraulic hose routing and installation techniques.
3. Pressure Surges
Causes:
- Sudden Pressure Increases: Rapid changes in system pressure can exceed the hydraulic hose’s rated capacity.
- System Design Flaws: Inadequate system design can lead to pressure surges.
- Component Failures: Malfunctioning components, such as valves or pumps, can cause unexpected pressure spikes.
Signs of Pressure Surges:
- Bursts: Sudden failures or bursts in the hydraulic hose.
- Leaks: Small leaks or weeping at fittings.
- Vibration: Increased vibration or noise in the system.
Mitigation:
- Pressure Monitoring: Use pressure gauges and sensors to monitor system pressure continuously.
- Relief Valves: Install pressure relief valves to protect against overpressure.
- System Design: Ensure the system is designed to handle expected pressure surges and has appropriate safeguards.
4. Fluid Compatibility
Causes:
- Incompatible Fluids: Using hydraulic fluids that are not compatible with the hydraulic hose material can cause swelling, degradation, or leaks.
- Contamination: Contaminants in the hydraulic fluid can damage the hydraulic hose.
Signs of Incompatibility:
- Swelling: The hydraulic hose may become enlarged or soft.
- Degradation: The hydraulic hose material may break down or become brittle.
- Leaks: Small leaks or weeping at the hydraulic hose surface.
Mitigation:
- Consult Specifications: Always consult the manufacturer’s specifications for fluid compatibility.
- Use Compatible Fluids: Ensure that the hydraulic fluid is compatible with the hydraulic hose material.
- Regular Fluid Testing: Test the hydraulic fluid regularly for contaminants and replace as needed.
5.The rubber layer is faulty
-The temperature is low, the temperature of cold objects in the environment plummets, and the hydraulic hose is no exception. Once the surface of the hydraulic hose cracks, the hydraulic hose will be bent. If there is a crack on the surface of the hydraulic hose, pay attention to whether there is a crack in the rubber in the hydraulic hose, and decide whether to replace the hydraulic hose immediately.
- Bubbling on the surface of the hydraulic hose. The appearance of the hydraulic hose bubbling is due to the quality of the hydraulic hose is not cooperative or improper use. If the bubble appears in the middle of the hydraulic hose, it is mostly a quality problem of hose production. Replace the qualified hydraulic hose in time; If the hose appears at the joint of the hose, it is likely due to improper installation of the joint.
-The hydraulic hose is not broken, but a lot of oil seepage. If the hydraulic hose is not found to be broken, but a large amount of oil is leaking, the reason is that when the high-pressure liquid flow in the hose, the inner glue is eroded and grazed until a large area of the steel wire leaks out resulting in a large amount of oil.
- The outer rubber layer of the hydraulic hose is seriously deteriorated, and the surface is slightly cracked. This is the hydraulic hose used for too long the natural aging performance.
6. The inner rubber layer is faulty
-The rubber layer inside the hydraulic hose is hard and cracked. Due to the addition of plasticizers to rubber products, the hydraulic hose is flexible and plastic. The hydraulic hose works under high temperature and high pressure, and the hydraulic hose overheats, which will make the plasticizer overflow. In addition, when the overheated oil passes through the cylinder, valve or other components in the system, if a large pressure drop is generated, the oil will decompose, causing the rubber layer inside the hydraulic hose to oxidize and harden. In this case, you should first check whether the working temperature of the hydraulic system is normal, the throttle of the valve, the oil suction channel of the pump is through, etc., and replace the hydraulic hose after excluding all factors that may lead to high oil temperature and oil decomposition.
-The rubber layer inside the hydraulic hose is seriously deteriorated and obviously swollen. The rubber layer in the hydraulic hose is seriously deteriorated, and the reason for the obvious expansion is that the hydraulic oil is used for a longer period of time or the dirt that is oxidized and deteriorated exists in the hydraulic system, the hydraulic hose is deteriorated by chemical action, and the broken rubber sheet will be found at the oil return port. If the phenomenon occurs, the physical and chemical indexes of the hydraulic oil should be checked, and the compatibility of the system oil in the rubber material in the hydraulic hoseand the working temperature meet the standard.
7. The hardening layer is faulty
-The hose is broken. The braided wire is rusty near the break. If the hose is broken, the outer rubber layer is peeled and the inspection finds that the braided and wound steel wire is rusty near the break, which is mainly due to the action of the wet or corrosive substances of the outer rubber layer, which exploitates the strength of the hose and causes the rupture at high pressure. This situation is generally accompanied by the phenomenon of fracture, abrasion or serious deterioration of the outer layer, so that the outer layer loses the protective effect of the strengthening layer. At this time, we must first check and eliminate the mechanical damage, chemical corrosion and high temperature baking and other adverse factors, and then replace the hose. However, there are also cases where the outer rubber layer is maintained well but the reinforcing layer rusts and breaks. And the rupture port is usually within 200mm from the hose joint, most of the reason is that the joint is unqualified, because the moisture enters the inner edge of the jacket, so that the strengthening layer absorbs moisture, resulting in rust caused by the hose pressure strength reduction and rupture.
-The hose strengthening layer is not rusty. However, if the hose is broken, the outer rubber layer is peeled and no rust is found in the reinforcement layer, but the irregular broken wire appears in the direction of the length of the reinforcement layer, mainly because the hose is affected by the high-frequency impact force. There are many crossing points between the steel wire and the steel wire. When the pressure in the pipe changes greatly, these crossing points also move with the change of the pipe diameter, which makes the steel wire rub against each other.
8.Fault at the fracture port
-The hydraulic hose is broken at one or more places, and the cracks are neat. The reason for this phenomenon is that the system pressure is too high, exceeding the pressure resistance of the hose. If the system pressure meets the requirements, check whether the actual pressure resistance of the hydraulic hose used meets the design requirements.
-The reason for this phenomenon is that the hydraulic hose is subjected to excessive torsion during installation or use. After the hydraulic hose is twisted, the structure of the strengthening layer is changed, the gap between the braided and wound steel wire is increased, which reduces the pressure strength of the hydraulic hose , and the hydraulic hose is easy to break under high pressure. Therefore, in the process of using or storing the hydraulic hose , the hydraulic hose should not be subjected to torsion torque, and the axis of the two joints should be on the same plane when installing the hydraulic hose , so as to avoid the hydraulic hose being twisted in use.
-Coil the wire at the hydraulic hose rupture. There is an obvious necking phenomenon. The reason for this phenomenon is that the hydraulic hose is subjected to excessive tensile deformation, and the layers are separated, reducing the compressive strength. Under the action of high pressure, the hydraulic hose will shrink or expand in the direction of length, and the general expansion amount is + 2% to -4% under normal conditions. If the hydraulic hose is selected too short during installation, it will be greatly stretched during work, and there will be failure such as rupture or loosening in serious cases; If the span of the hydraulic hose is too large, the hydraulic hose weight and oil weight will also give the hydraulic hose a large tensile force, and the above failure will occur in serious cases. Therefore, the appropriate solution should be taken according to the specific situation. If it is pulled too tight during installation, it should be replaced with a lengthened new tube; If the span is too large, the middle support clip should be added.
Additional Best Practices
- Training and Education: Ensure that all personnel involved in the installation, maintenance, and operation of hydraulic systems are well-trained and knowledgeable about best practices.
- Documented Procedures: Maintain detailed records of all maintenance activities, including inspections, repairs, and replacements.
- Regular Maintenance: Follow a regular maintenance schedule to inspect, test, and replace hoses as needed.
- Emergency Preparedness: Have a plan in place for emergency situations, including spare parts and trained personnel to handle hydraulic hose failures.
- The hydraulic hose has a very short life when working at high temperatures. Therefore, the hose layout should be as far away from the heat source as possible, and the installation of sleeve or heat insulation plate can be used when forced to avoid the deterioration of the hydraulic hose by heat.
-When installing the hose, do not contact with other hoses or piping to avoid wear and tear. Where the hydraulic hose must cross or where the work may rub against the mechanical surface, protective devices such as hydraulic hose clamps or springs should be used to avoid damage to the outer layer of the hose.
By addressing these factors and implementing best practices, you can significantly reduce the risk of hydraulic hose failure and ensure the safe and efficient operation of your hydraulic systems.
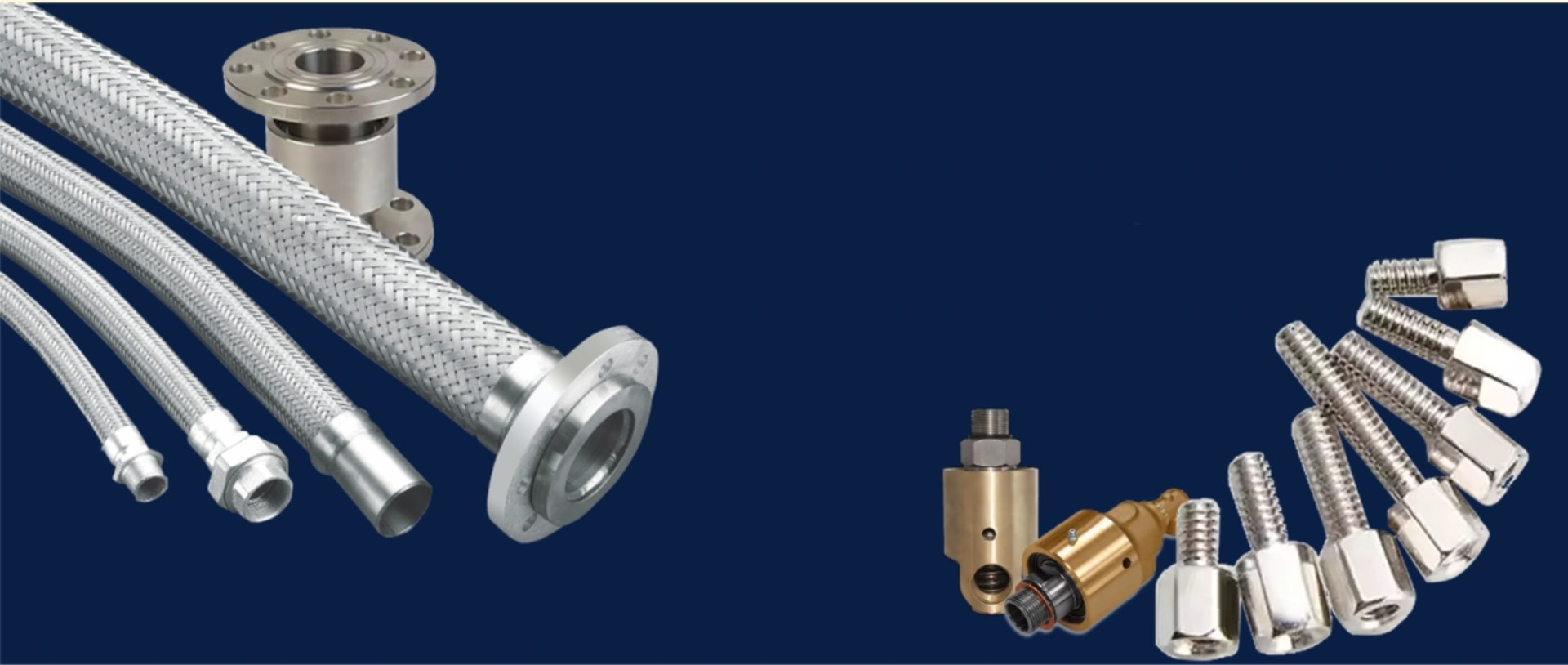