One stop hydraulic hardware product service provider Rotary Joint HYDRAULIC HOSE HOSE FITTING
WHAT IS THE IMPORTANCE OF PROPER HYDRAULIC HOSE ROUTING?
HYDRAULIC HOSE
4 min read
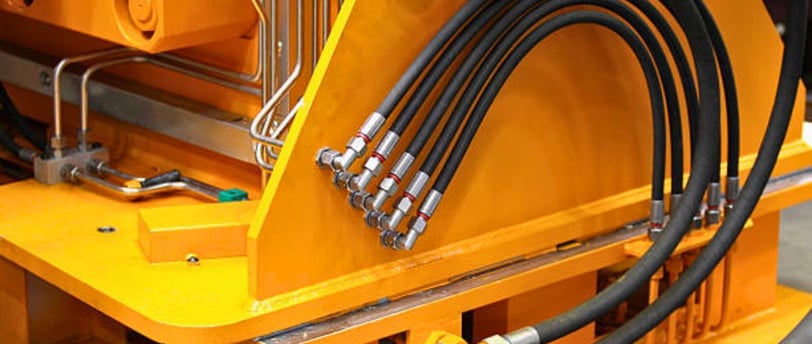
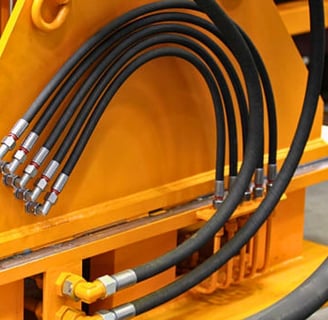
Hydraulic hose is an important part of hydraulic system, and its correct installation and use is very important to the stability and efficiency of the hydraulic system. The purpose of this guide is to provide guidance for the installation of Hydraulic hose to help users correctly select, install and use Hydraulic hose to ensure the normal operation of the hydraulic system.Proper routing of Hydraulic hose is crucial for maintaining the efficiency, safety, and longevity of hydraulic systems. Here's a more detailed look at why each of these points is important:
1. Planning and design
System diagram: Before wiring, draw a detailed system diagram, including the location and connection of all components.
Path planning: Plan the path of Hydraulic hose to ensure they are away from heat sources, sharp edges, and other potential sources of damage.
Length calculation: Ensure that the Hydraulic hose has sufficient length to accommodate the movement of moving parts while avoiding slack and winding caused by excessive length.
2. Select the appropriate Hydraulic hose and connector
Material and specification: Select the right Hydraulic hose and fitting material based on the system's operating pressure, temperature and fluid type. Commonly used materials include rubber, PVC, polyurethane and so on.
Size and length: Select the right inner and outer diameter Hydraulic hose to ensure smooth fluid flow and minimal pressure loss. Measure the required length to ensure that the hose is neither too long nor too short.
Joint type: Select the appropriate joint type, such as straight joint, elbow joint, quick joint, etc., to ensure that the connection is solid and reliable.
3. Prepare for installation
Cleaning: Before installation, ensure that all Hydraulic hose and fittings are clean and free of dust, oil and other impurities.
Inspection: Check Hydraulic hoses and joints for damage, cracks or other defects to ensure they meet quality standards.
4. Wiring and fixing
Routing path: Route the Hydraulic hose according to the pre-planned path to ensure that the Hydraulic hose is straight, without distortion or excessive bending.
Fixing: Use clamps, clamps, or other fixing devices to hold the Hydraulic hose in place to avoid damage from vibration or movement.
Spacing: The distance between fixed points should be moderate, usually fixed every 30-50 cm.
Avoid stress concentration: Ensure that the fixed point does not cause excessive stretching or compression of the Hydraulic hose.
Protection: Use a sheath or shield to protect the Hydraulic hose when it passes through sharp edges or hot areas.
5. Connect and test
Connection: Attach the joint to the assembly using a suitable tool, such as a torque wrench, according to the manufacturer's recommended torque value.
Exhaust: Before the system starts, exhaust the air in the system to ensure smooth fluid flow.
Pressure test: Before the system is run, a pressure test is performed to check for leaks at all connection points.
Step pressure: Gradually increase the system pressure to observe whether there are leaks or abnormal conditions.
Check for leaks: Use a leak detector or soapy water to check the connection points to ensure there are no leaks.
6. Maintenance and inspection
Regular inspection: Check Hydraulic hoses and joints regularly to make sure they are not worn, cracked, or leaking.
Replacement: Promptly replace any damaged or aged Hydraulic hoses and fittings to avoid system failure.
Records: Maintain detailed maintenance records, including replacement dates, reasons, and materials used.
7. Safety precautions
Personal protection: Wear appropriate safety equipment, such as safety glasses and gloves, during installation and maintenance.
Compliance with standards: Compliance with relevant industry standards and safety specifications such as ISO, SAE, etc.
Training: Ensure that all operators receive proper training on proper wiring and maintenance methods.
Example: Hydraulic Hydraulic hose wiring steps
Planning path:
Draw a diagram of the system, marking where all components are and how they are connected.
Plan the path of the hose, making sure it is away from heat sources and sharp edges.
Select Hydraulic hoses and fittings:
Select the appropriate Hydraulic hose material and specifications according to the operating pressure and temperature of the system.
Select the appropriate joint type to ensure a strong and reliable connection.
Preparation before installation:
Clean Hydraulic hoses and connectors to ensure they are free of dirt and oil.
Inspect Hydraulic hoses and joints for damage or defects.
Wiring and fixing:
Route the cables along the planned route to ensure that the Hydraulic hoses are straight and without distortion.
Use clamps or clamps to hold the Hydraulic hose in place every 30-50 cm.
When passing through sharp edges or high temperature areas, use a sheath or shield for protection.
Connection and test:
Attach the joint to the assembly using a torque wrench to ensure that the recommended torque value is achieved.
Perform venting operations to remove air from the system.
Gradually increase system pressure and check all connection points for leaks.
Maintenance and inspection:
Check Hydraulic hoses and joints regularly to ensure no wear, cracks or leaks.
Promptly replace any damaged or aged Hydraulic hoses and fittings.
Maintain detailed maintenance records.
Additionally, proper Hydraulic hose routing contributes to easier maintenance and inspection, as well-organized hoses are easier to access and assess for signs of wear or damage. It also enhances the overall appearance and professionalism of the installation, which can be important in industrial settings where safety and reliability are paramount.
To achieve proper routing, consider the following best practices:
- Use Hydraulic hose guides and clamps to keep Hydraulic hoses organized and secure.
- Ensure there is enough clearance between Hydraulic hoses and other components to avoid rubbing.
- Avoid sharp bends by using appropriate bend radii.
- Plan the route to minimize the length of Hydraulic hose used while still providing enough flexibility.
- Regularly inspect Hydraulic hoses for signs of wear, damage, or misrouting.
By adhering to these guidelines, you can ensure that your hydraulic system operates efficiently and safely, with minimal downtime and maintenance costs.
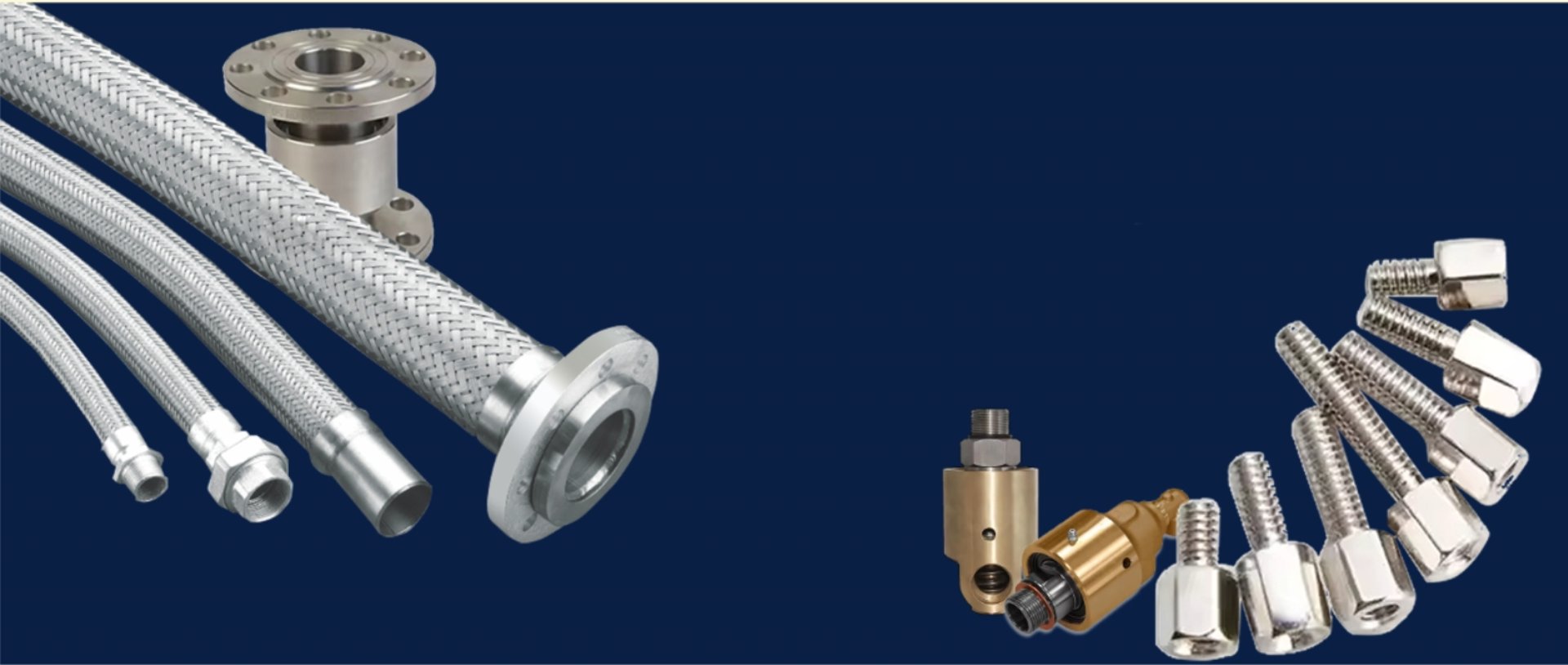